Whipped into shape
- By Spencer Kay
- Feb 01, 2001
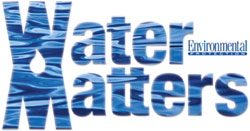
With the installation of a new chemical induction system, the West Basin Water Reclamation Plant substantially improved chemical mixing efficiency while eliminating difficulties of meeting strict chlorine residual requirements.
Maintaining a stringently high chlorine residual requirement proved difficult for operators at the West Basin Water Reclamation Plant in Los Angeles County, Calif. However, through the adoption of high energy chemical induction, this problem was solved while sodium hypochlorite usage was reduced by more than 35 percent. High energy mixing has since been added to three additional chemical induction points at the facility, improving efficiencies in these areas and providing further reductions in chemical usage.
The West Basin Water Reclamation Plant is one of the largest water-recycling projects in the world. The facility currently recycles approximately 25 million gallons per day (MGD) of wastewater from the City of Los Angeles' Hyperion Treatment Plant. The goal of West Basin Municipal Water District's recycling program is to ultimately recycle 100 MGD of Hyperion Treatment Plant effluent.
A reduction in chemical usage of just a few percentage points can add up to tens of thousands of dollars in annual savings at a large plant. |
Eighty percent of southern California's water comes from outside the region. These sources are dwindling, and their reliability is uncertain. The area also suffers from extended drought conditions. The West Basin Municipal Water District has determined that the best way to address the growing shortage of fresh water in the area is to extend of existing water supplies through recycling.
System overview
The facility processes and distributes recycled water through two distinct treatment processes, resulting in "Barrier" and "Title 22" water. Barrier water is used to protect the South Bay's coastal groundwater reservoirs against saltwater intrusion from the Pacific Ocean. A series of wells constructed along the coast form a freshwater barrier to prevent intrusion. Fifty- percent potable water, along with 50 percent recycled Barrier water from the plant, is injected into the wells to protect the groundwater table. Barrier water from the facility meets U.S. Environmental Protection Agency (EPA) standards for drinking water.
Title 22 refers to the section of the California Code of Regulations that addresses recycled water quality standards. Title 22 water produced at the plant can be used in a variety of industrial and irrigation applications where high quality, but not necessarily potable, water is required.
Title 22 water is produced through coagulation/flocculation followed by filtration through a set of anthracite coal media filters. Following filtration, the water goes through a disinfection stage, whereby sodium hypochlorite is added before the water enters chlorine contact basins and is retained for at least 90 minutes to ensure adequate disinfection.
Once the water has been disinfected, it is sent to a five-million-gallon storage reservoir, where it is then distributed through the West Basin Title 22 Distribution System. The system is connected to recycled water users throughout the South Bay area, including parks, golf courses, schools, cemeteries, green belt areas, as well as oil refineries and other industrial users.
High chlorine residual requirement
When the plant came on-line in 1995, operators found it difficult to maintain the required chlorine residual for Title 22 water, which is 5.6 milligrams per liter (mg/L) to 6.0 mg/L. As a result, the plant injected significantly high dosage rates of sodium hypochlorite in order to consistently meet the high residual requirement.
Hypochlorite use for Title 22 water was reduced by 35 percent due to more efficient chemical mixing. |
The plant's original sodium hypochlorite dispersion system was a "flash mixer" of conventional design, which incorporated an injector and mechanical paddle mixer to feed sodium hypochlorite to flows entering the contact basins. Facility management eventually determined that increasing and optimizing mixing energy would better ensure thorough chemical induction and dispersion. In addition, operators felt that more thorough mixing in this application would help prevent deposition of solids in the contact chamber, which would further increase chemical efficiency.
In 1998, the facility replaced the original mixing system with an in-line chemical induction unit that is capable of inducing the chemical directly into the process stream at velocities of up to 60 feet per second (ft/sec). The new Water Champ® Chemical Induction Unit (CIU), developed by USFilter's Stranco Products, Bradley, Ill., operates on the simple principle of applying all available energy directly to the chemical being activated.
The unit design includes a five-horse power (hp) chemical processing duty motor mounted to the in-line unit with a vacuum body and airfoil design propeller at the other end. Chemical solution is injected into the body of the unit and is dispersed into the channel, while simultaneously mixed through this open propeller. The unique airfoil design of the titanium propeller rotates at 3,450 revolutions per minute (rpm), enabling the unit to achieve high energy transfer. The motor-driven open propeller creates a vacuum in the chamber directly above the propeller. This vacuum is transmitted to the chemical metering system by a vacuum line.
A Water Champ CIU was installed in the 42-inch effluent pipe (following mono-media filtration in the Title 22 process stream) using a packing gland/knife gate valve arrangement. This allowed the unit to be installed into the closed conduit to maximize the chemical induction/mixing process, positioned perpendicular to the conduit. From the sodium hypochlorite bulk tanks, a chemical metering pump feeds the chemical feed line leading to the in-line unit.
Positioned downward into the flow regime, the chemical induction unit provides a zone of influence across the influent conduit discharge, creating a highly turbulent axial flow pattern that extends away from the propeller outward into the process flow. This generates high zone diffusion and a high turbulence region as sodium hypochlorite is simultaneously dispersed. Flows passing the mixing area make contact with this turbulence and distributed chemical, resulting in a high rapid mixing rate.
Chemical induction: The key
Because the new high energy induction unit provides a more homogenous solution of chlorine residual within the entire contact basin than the previous system, the plant immediately reduced the dosage of sodium hypochlorite required to achieve the relatively high effluent chlorine residual of 5.6 mg/l to 6.0 mg/l. Hypochlorite use for Title 22 water was reduced by 35 percent due to more efficient chemical mixing, thereby providing a simple payback for the new mixer in its first 60 days of service.
The switch to the high-energy chemical induction unit has substantially improved algae control. |
Due to the increased efficiency brought about by the installation of the original Water Champ CIU, three additional units have since been installed at the West Bay Water Reclamation Plant.
One of the in-line chemical induction units has been installed to feed coagulant prior to flocculation. The competitive nature of the chemical reactions that precede charge neutralization in the coagulation/flocculation stage of the Title 22 process stream makes it imperative that the coagulant be dispersed as rapidly as possible. The new in-line chemical induction system now provides effective activation of the chemical for maximizing liquid/solid separation.
A submersible CIU was installed in an open channel of one of the Barrier water process trains for algae control prior to tri-media filtration. Previously, the chemical was simply injected just prior to filtration with no mixing. The switch to the high-energy chemical induction unit has substantially improved algae control.
Facility management eventually determined that increasing and optimizing mixing energy would better ensure thorough chemical induction and dispersion. |
High energy chemical induction has also significantly reduced sodium hypochlorite use for disinfection in one of the plant's Barrier water process streams. Water for the Barrier process is made up of two treatment methods - conventional and microfiltration/reverse osmosis(RO). A Water Champ CIU was installed in the microfilter/RO process train following RO. The water proceeds into a chlorine contact basin where, similar to the Title 22 process, it is retained for at least 90 minutes to ensure adequate disinfection. Chlorine residual requirements for Barrier water produced through the microfiltration/RO process are also high - 4.1 mg/l to 4.5 mg/l. The introduction of high-energy chemical dispersion has allowed the plant to meet this stringent requirement while also achieving significant chemical savings, similar to the reduction achieved for the facility's Title 22 water disinfection.
Conclusion
After power costs, chemical disinfection typically represents the single largest consumable expenditure at a wastewater treatment facility. A reduction in chemical usage of just a few percentage points can add up to tens of thousands of dollars in annual savings at a large plant. Inefficient chemical mixing can lead to inefficient oxidative disinfection, bringing with it higher costs. However, by placing properly engineered, high mixing energy directly to the chemical being activated, The West Basin Water Reclamation Plant has significantly improved chemical efficiency and reduced chemical usage accordingly.
This article originally appeared in the 02/01/2001 issue of Environmental Protection.
About the Author
Spencer A. Kay is president, CEO and founder of Fastrack Healthcare Systems in Plainview, N.Y. Founded in 1994, Fastrack offers Windows-based solutions for HME and respiratory providers and solutions for home infusion and home health care agencies. Kay holds an MBA in International Business from George Washington University and a BA in Economics, and has more than 25 years of technology related experience. Visit www.onlyfastrack.com.