Case Study: Dry Scrubber Lowers Energy Costs for Spray Booth
- By Jim Pakkala
- May 06, 2010
A spray booth equipped with EcoDryScrubber.
In automotive paint finishing operations, between 40 and 50 percent of the energy required to make an automobile is consumed by equipment that handles and conditions process air for the spray booths. By re-circulating a substantial portion of air exhausted from the spray booth back to the painting chamber, companies could lower energy requirements and related costs.
Spray booths typically use wet separation technology (wet scrubbers) that capture paint overspray particulate with a chemically treated water curtain. Although wet scrubbers can yield separation efficiencies well above 99 percent, paint particulate concentrations in their exhaust air streams are far above acceptable levels for painting environments. A wet scrubber also humidifies process air to near-saturation. To implement an air recirculation scheme in this case would require installing high efficiency bag filters and dehumidification equipment downstream to further clean and re-condition the process air.
More than 24 original equipment manufacturers in Europe and China have purchased an energy-saving technology ─ EcoDryScrubber ─ that uses a regenerative dry process that allows for recirculation of spray booth process air without the need for additional air conditioning equipment. Now, the topcoat line of the new $1 billion Volkswagen assembly plant in Chattanooga, Tenn., will be the first full car body spray booth in North America equipped with the process, which was developed by Dürr.
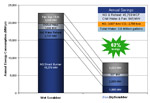
Example of Potential Energy and Environmental Savings Chart. Click to enlarge (PDF).
The EcoDryScrubber directs paint-laden process air into scrubber chambers below and on either side of the painting chamber. Each scrubbing chamber contains an array of porous plastic filter elements. To protect the filter elements from fouling, the process automatically applies a sacrificial layer of milled calcium carbonate to the exterior of each filter element in a process referred to as pre-coating. As the air is drawn through the scrubber chambers and across the filter elements, the pre-coat layer captures wet paint particles. Paint solid particulates accumulate within the pre-coat layer until the systems measures a predetermined pressure loss. The pressure loss triggers a back pulsing sequence that releases the now fouled pre-coat layer from the filter elements. The fouled material, which is completely dry and free-flowing, is collected and automatically removed from hoppers below the filter elements. Virgin pre-coat material is then introduced into the scrubbing chamber and the process is repeated.
The fouled waste material, typically classified as nonhazardous, can be directly recycled into cement products. As compared to wet scrubber water treatment, chemical and sludge disposal costs, the costs of supplying and recycling the pre-coat are between 20 and 40 percent lower.
By using the EcoDryScrubber, energy usage at the Volkswagen top coat spray booth is estimated to be on average 14,000 MW/yr less (62 percent reduction) than that of a traditional spray booth. Included in this savings will be a 45 million ft³/yr reduction in natural gas usage. This reduction will translate into lower carbon dioxide and nitrogen oxide emissions by 2,800 ton/year and 3,800 lbm/yr, respectively. The plant's water usage also will be lowered by nearly 4 million gal/yr.
According to Volkswagen's Web site, the energy-saving assembly plant will begin production in 2011. The company plans to produce a new mid-size sedan designed for the United States; 30 percent of which will be powered by Volkswagen's TDI Clean Diesel technology. The plant can make up to 150,000 cars a year.
About the Author
Jim Pakkala, P.E., is an engineering manager at Dürr Systems' Paint and Final Assembly Systems in Plymouth, Mich.