Aboveboard Compliance
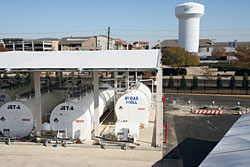
"Compliance with EPA
Regulations AT New Bulk Fueling Facility for Addison Airport - Addison, Texas"
The Addison Airport (ADS) is located in a closed-in suburb of Dallas, Texas
and logged 133,000 operations in 2005. With a 7,200-foot runway, Addison is
the preferred choice among owners of private aircraft and corporate jet fleets
because of its convenient access to downtown Dallas, the Telecom Corridor, and
other large employment centers.
Emphasizing a business-friendly atmosphere and recognizing the needs of the
aviation community, Addison Airport has set industry standards for safety, economy,
and convenience. Initially developed by a group of flying enthusiasts in 1957,
Addison Airport has been owned by the Town of Addison since 1976 and is the
second busiest general aviation airport in Texas.
The NPDES Stormwater
Program
The Airport's de-icing and fueling facilities are specifically identified as
industrial activities subject to comply with the U.S. Environmental Protection
Agency (EPA) Regulations. The 1972 Amendments to the Clean Water Act prohibit
discharge of any pollutants into waters of the United States from a point source
unless the discharge is authorized by a National Pollutant Discharge Elimination
System (NPDES) permit. The NPDES permitting program has been established to
monitor the discharge of pollutants from point source stormwater runoff and
requires the use of necessary controls to minimize the discharge of pollutants.
EPA requires facilities that engage in regulated industrial activities to obtain
NPDES permits. The term "Storm Water Discharges Associated with Industrial
Activity" is defined in the Code of Federal Regulations 40 CFR 122.26,
and determines which industrial facilities are potentially subject to Phase
I of the NPDES stormwater program. The program typically identifies these industrial
activities through the use of SIC (Standard Industrial Classification) codes.
Also, due to the large fuel storage capacity necessary to maintain transportation
activities at the airport, the new bulk fuel facility at Addison Airport was
required to meet EPA's Spill Prevention Control and Countermeasure (SPCC) requirements.
The SPCC rules require facilities that meet the aboveground oil storage capacity
threshold of 1,320 gallons or more to prepare an SPCC plan. The SPCC plan is
typically designed by an engineer and describes actions the facility must take
to prevent oil spills from reaching navigable waters of the United States. The
SPCC requirements almost always apply to airport facilities due to the large
quantities of fuel being stored.
Out With the Old
With the increasing numbers of aircraft making their home at Addison and a higher
frequency of daily flights, airport officials determined that it was time to
replace the ageing underground fuel storage facility. Their concept was to design
and build a state-of-the-art refueling facility using the best available aboveground
storage technology. The result is a sweeping wing-like canopy covering twenty-one
aboveground steel storage tanks.
The Washington Group was the lead engineering firm on the design of the new
aboveground bulk fuel storage facility at the airport. The fuel storage facility's
design required 330,000 gallons of aboveground storage capacity, which triggered
compliance under the SPCC rules. The Washington Group decided to go with double-walled
steel tanks. The Group's engineers specified nine 25,000-gallon, six 15,000-gallon,
and five 300-gallon cylindrical tanks. The facility is designed to store Jet-A,
Diesel, and AVGAS fuels for the many types of aircraft operating from Addison.
The project specifications also included a 10,000-gallon high-performance oil/water
separator. The oil/water separator was installed to remove any hydrocarbons
that may contaminate the stormwater runoff from the tank-farm dike drainage
system. The Thielsch Engineering Company was selected to complete procurement
and installation of the project.
The Washington Group engineers specified the use of thermally protected, double-walled
aboveground tanks because they utilize the best available technology and are
Underwriters Laboratories (UL)-2085 and UL-142 approved.
The oil/water separator
tank selected for the project to treat the tank farm dike drainage was also
state-of-the-art. The separator system was installed to satisfy the airport's
NPDES permit. It was designed for the treatment of contaminated stormwater runoff
at 0 to 1,000 gallons per minute discharging with a qualified / certified effluent
quality of 10 parts per million (ppm) of free oil and grease. The separator
meets the new Underwriter's Laboratories Inc. SU2215 design, construction, and
performance standards for engineered oil/water separators rated at 10-ppm oil
and grease. Currently, code enforcement officials consider UL-SU2215 certification
as being the pre-eminent national consensus standard for oil/water separator
construction and performance.
The design engineers and the installer have made every effort to ensure that
the new bulk fuel storage facility at Addison Airport will offer no threat to
the surrounding community. Well-maintained ASTs should ensure there will be
no accidental releases of fuel being discharged in the facility's stormwater
runoff.
Tough Tanks
The aboveground tanks' insulation provides thermal protection for the inner
tank in the unlikely event of a pool fire or other extreme heat. The insulation
material is porous and allows fluid migration through the interstice to
the monitoring sensor. Unlike outdated concrete encased tanks, the steel
outer wall protects the insulation, eliminating the problem of cracking
concrete. The insulation material is lightweight (on average, 75 percent
lighter than concrete) and costs less to ship and install. The double-wall
design allows a pressure-testable primary and secondary tank per the National
Fire Protection Association's (NFPA) 30 requirements. The tanks' design
also has emergency vents on the primary and secondary tank. This advanced
tank design has been tested and approved to meet the UL 2085 requirements
for a two-hour fire rating and has completed the Uniform Fire Code (UFC)
AST testing procedure that requires four tests be completed before they
designate a tank as "protected" for use. The tests include:
- Ballistics Test:
The tank must withstand five rounds of 150-grain M-2 ball ammunition
without having the primary tank penetrated.
- Impact Test: The
protected tank must withstand a blow by a 12,000-pound mass, traveling
10 miles per hour, without penetrating the primary tank.
- Two-hour Pool
Fire Test: The internal temperature of the tank during the two-hour
test cannot exceed 260 degrees Fahrenheit average temperature rise,
or 400 degrees Fahrenheit maximum temperature at a single point in the
tank.
- Hose Stream Test:
The tank must withstand the impact, erosion, and cooling effects of
a hose stream without penetrating the primary tank.
The chosen tanks
had previously passed a battery of tests required by Underwriters Laboratories
(UL) to receive the UL 2085 listing for "Insulated Secondary Containment
Aboveground Tank for Flammable and Combustible Liquids". The UL testing
also included a two-hour fire test (see figure 2), interstitial communication
test, and proof-of-emergency-venting capabilities. The tanks are now approved
for motor fuels storage under every National fire code, including the
Uniform Fire Code (UFC), NFPA 30, NFPA 30A, Southern Building Code Congress
International (SBCCI), Standard Fire Prevention Code (SFPC), Steel Tank
Institute F941 "Standard for Thermally Insulated Aboveground Storage
Tanks," and 1993 Building Officials and Code Administrators (BOCA). |
This editorial originally appeared in the September 2006 issue of Environmental
Protection, Vol. 17, No. 7
This article originally appeared in the 09/01/2006 issue of Environmental Protection.
About the Author
Stephen R. Verbit, Esq., is an environmental attorney in private practice in Miami/Fort Lauderdale, Fla.