Greening the Big Apple
- By Richard MacLean
- Oct 01, 2002
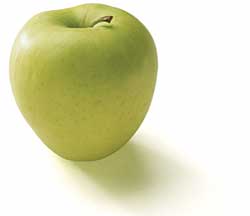
Consolidated Edison (Con Edison) has had its share of serious environmental problems. The programs and strategies that have evolved as a result of these issues have received little recognition in the mainstream press and even less in environmental magazines and journals. The company has developed unique approaches to environmental health and safety (EHS) management that provide an interesting benchmark, especially in these times of increased attention to governance.
I have searched in vain for the company that has truly excelled in environmental leadership -- pushed the envelope, so to speak -- that did not either go through hell or was pushed forward by a single individual, usually a visionary CEO. Con Edison unwillingly chose the route through hell.
In 1989, a steam pipe explosion in the Gramercy Park area of Manhattan released approximately 200 pounds of asbestos into the air. Many people had to be evacuated from their homes during the cleanup operation. Con Edison and two of its officers were indicted on various charges, including conspiracy to conceal the fact that asbestos was present. In 1994, the company pleaded guilty and was fined $2 million. A federal judge placed the company on probation and appointed a staff-attorney with the Natural Resources Defense Council (NRDC) to monitor all company environmental operations.
The company had been released from probation only a few months when, in 1998, a fire in a transformer at the Arthur Kill Generating Station released polychlorinated biphenyls- (PCB) containing oil into the Arthur Kill-adjacent tidal wetlands and marine surface waters. Con Edison was late reporting the presence of PCBs and was forced to pay penalties and fines totaling nearly a million dollars. These problems resulted in a number of unique regulatory constraints and consent orders. Following the Arthur Kill incident, the court-appointed monitor returned for two more years as a "consultant" to the U.S. Attorney for the Southern District. Not only was the company placed under the regulatory microscope, but it came under the spotlight of the country's major media centers based in the Big Apple. The heat was on (See "Burning Platforms" sidebar).
A Strategy Emerges
Most of the executive leaders at Con Edison are trained engineers. They realized that they had fundamental failures in their control systems. Instead of countering the problems by ramping up the public relations, they began a program to systematically address the weaknesses in 1994.
An officer-level position was created in 1995 to lead this effort and staffing was increased dramatically between 1995 and 1997. This included upgrading the company's environmental laboratory to improve both the quality and turnaround time in sample analysis. The race to improve the systems began in 1995 and culminated in company-wide certification under ISO 14001 in February 2002. Lloyds of London is the registrar.
None of the preceding information is particularly unusual in the wake of a major issue. What is unique at Con Edison is executive management's interaction with the environmental staff and its approach to environmental strategic planning (see "The Strategic Planning Challenge" sidebar).
In 1995, Robert Shelton first used the term "Green Wall" to describe the wall separating the environmental managers from business executives.1 Environmental managers generally agree that one of the most important elements for successful program implementation and impact within a company is access to the business leaders who made the critical decisions. All too often, environmental managers are in a reactive mode responding after the fact to newly created issues, when management has already made their minds up on an acquisition, new product or process introduction.
Con Edison's vice president of EHS, Randy Price, has a direct reporting relationship to the president and to the chairman of the board of directors. I know of no other EHS manager who has this duel reporting relationship in a major corporation. Most are separated by at least one layer from the CEO and have little formal connection to the chairman. Lines on an organization chart are cheap; however, I was more impressed with the substance behind the chart.
The vice president of EHS is an officer of the corporation (i.e., listed with the U.S. Securities and Exchange Commission (SEC)), not merely someone holding a title. In addition, there is a stand-alone environmental committee of the board of directors consisting of four external directors, and the chairman. The president of the company and the general counsel also attend. In many companies, this governance function (if it exists at all) is combined with other board functions, such as the finance or audit committees. These meetings last one hour or more, four times each year. The EHS vice president also sits on the bi-weekly senior executive management staff meetings with the president.
There is a monthly meeting of the environment and safety committee consisting of the senior officers. This meeting lasts two hours -- a phenomenal amount of executive management time. I know EHS managers who consider themselves lucky to get one hour of the CEO's time per year. In addition to the face-to-face communication, there is a very detailed monthly management report, complete with graphs that track performance metrics. Recently, the company introduced a cover summary page that allows the officers to instantly see the current status and trend data on key performance indices.
Pulling the Pieces Together
A much more subtle point (but one that is not lost among my colleagues) in management's commitment to "get the company's act together" is that when the previous EHS vice president retired in 2001, they replaced him with a seasoned veteran. Unfortunately, the trend in most companies has been to bring in an attorney (circle the wagons), a communications expert (talk your way out of it), a former regulatory official (it's only about compliance) or an inexperienced "safe person" (someone management can easily control). Randy's background in EHS goes back 25 years with management-level experience with DuPont and Honeywell (formerly AlliedSignal).
Randy joined Con Edison in August 2001, literally days before the World Trade Center terrorist attack occurred just blocks away from his Manhattan office. The issues created by that disaster consumed him for several months. Beginning in November 2001, his attention turned to strengthening the strategic plan by linking the management system components together. He emphasized, "The basic components pre-dated my arrival. This is what made the job relatively easy and doable in a short period of time. What we have done is develop a structure to the EHS plan that maps the business strategy."
After clearly defining the EHS function's mission in support of the business, six key objectives were identified that fell into four categories:
1) Liability Reduction,
2) Stakeholder Relationships,
3) Performance Improvement and
4) Culture Change.
These categories were matched against the individual management system components consisting of 14 major systems and 55 sub-components. Each sub-component was rated according to its
1) Relationship with business goals,
2) Significance to achieving the objectives,
3) Effectiveness and
4) Efficiency.
What is particularly interesting (and unique) is the way that the EHS objectives closely parallel the business objectives and support individual programs, such as the company's "The Way We Work" culture change effort. Most strategic plans are nothing more than task lists with "high/medium/low" priorities assigned. The Con Edison mapping process makes it much easier for management to see the value of the individual elements (through the ranking system), as well as how the components fit together. The strategy has been reviewed with the officers of the company as well as the Environmental Committee of the Board.
Conclusions
Con Edison, as with most corporations, is far from the day when future incidents are all but impossible, but it has two critical components that most do not: a cohesive strategy and no "green wall" between EHS management and business executives. Success in the future will depend to a major extent on a continuing culture change from "it's the EHS department's responsibility" to "it's all of our responsibility." Culture change starts at the top, and the access that Con Edison management provides to these audiences is commendable.
Burning Platforms
Many of my colleagues in industry management positions owe their positions to major screw-ups that they were called in to straighten out. These "burning platforms" provided the resources and the management access to do what most companies had no interest in pursuing. Royal Dutch Shell had Brent Spar (i.e., the 1996 incident involving Greenpeace's protest concerning Shell's intent to dump the Brent Spar Oil installation in the North Sea near Great Britian). Today, they receive accolades from non-governmental organizations (NGOs) for their stakeholder outreach. Union Carbide had Bhopal (In 1984, the Union Carbide plant in Bhopal, India, has an accidental release of the toxic chemical methyl isocyanate, causing the deaths of more than 2,000 people and adverse health effects in approximately 170,000 survivors.), and for the decade that followed, they were the company to use for auditing practices benchmarking. The list goes on and on and on.
I believe that most corporations that go through a truly traumatic experience institute systems that become part of the ingrained systems and polices, if not the cultural fabric of the company. This is not always the case when a leadership position is taken by the CEO. For example, Maurice Strong led Ontario Hydro as a champion for sustainable development. The programs were abandoned as soon as he left the company.2
Regardless of the motivating force behind a leap forward, the fact remains that these companies define the path for others to follow. The McDonald's partnership with Environmental Defense set the stage for other NGO/company relationships. Dow set the model for international environmental due diligence with the acquisition and reconstruction of BSL (Buna Sow Leuna Olefinverbund GmbH), the former East German chemical industry giant. And so it goes.
A burning platform is not, however, a guarantee that forward progress is assured. General Electric (GE) has its Hudson River. GE is the only responsible party at the Hudson River Superfund Site in New York and now must pay an estimated $460 million to dredge the river to remove large amounts of PCBs that were released by the company. But if anything the company seems more entrenched than ever in legal posturing rather than proactive programs. Much depends on executive management's personal views of the environment and their responsibility to society, not just shareholders and employees. Some just turn up the public relations volume -- a risky strategy if the systems continue to be inadequate and the next issue hits. I have even run across cases where executive management is so disconnected from reality that they rationalize away a major past issue as a "one-time" deviation that will never repeat. Again, a risky position.
The Strategic Planning Challenge
In the April 2002 issue of Environmental Protection, I challenged readers with, "If any "Manager's Notebook" reader is aware of a Board of Directors presentation within their company devoted to a detailed review of the company EHS strategic plan (i.e., not just a specific issue or project review), call me and I'll buy you dinner."
So here we have the results: The challenge went out to nearly one hundred thousand readers of Environmental Protection across the country and only one company made the cut: Consolidated Edison. I did receive one other inquiry for a national government research lab that claimed to have a review "every five years" with their directors, but when questioned if this was a detailed report, not just a project review, they fell by the wayside.
There may be others out there but, if anything, this challenge lends proof to my original statement that good EHS strategic planning is rare and even rarer are those plans that get adequate review at the upper echelons where they would do the most good.
The article this month grew out of the discussions I had with Randy Price, vice president, Environmental, Health and Safety, when I traveled to New York City to make good on my promise. And you thought I was joking?
References
1
Robert Shelton, "The Role of Upper Management," Chapter 2, Environmental Management and Business Strategy: Leadership Skills for the 21st Century, Edited by B. Piasecki, et al., John Wiley & Sons, 1998, Page 10.
2
N. Roome and R. Bergin, "The Challenges of Sustainable Development: Lessons From Ontario Hydro," Corporate Environmental Strategy, Elsevier, Vol. 7, No. 1, Pages 9-19.
This article originally appeared in the October 2002 issue of Environmental Protection, Vol. 13, No. 9, p. 12.
This article originally appeared in the 10/01/2002 issue of Environmental Protection.
About the Author
Richard MacLean is president of Competitive Environment Inc., a management consulting firm established in 1995 in Scottsdale, Ariz., and the executive director of the Center for Environmental Innovation (CEI), a university-based nonprofit research organization. For Adobe Acrobat® electronic files of this and his other writings, visit his website at http//:www.Competitive-E.com.