Keeping Hazardous Materials Contained
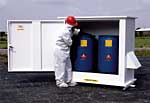
Government regulations place the responsibility for damage caused by leaks or spills of chemicals or other hazardous materials squarely on your shoulders whether you are a facility that accumulates, transports, treats or disposes of these substances. Wisdom dictates that you take all prudent precautions to minimize such damage and avoid liability for a discharge under Comprehensive Environmental Response, Compensation and Liability Act (CERCLA), also known as Superfund, or state statute. The terms hazardous materials, hazardous chemicals and hazardous waste tend to be used interchangeably although their definitions are actually very different.
"Hazardous materials" are raw materials governed by the U.S. Department of Transportation (DOT) while in transit to a user. Included are any substances that may pose an unreasonable risk to health, safety or property as determined by the Secretary of Transportation.
A hazardous material is defined as a "hazardous chemical" when it arrives at its destination and is used in the workplace. As such, it is regulated by the U.S. Occupational Safety and Health Administration (OSHA) under 29 Code of Federal Regulations (CFR). A "hazardous waste" is generated by a process. A hazardous chemical becomes a hazardous waste once it completes its useful life and is ready for disposal. At this stage, it is regulated by the U.S. Environmental Protection Agency (EPA) under 40 CFR.
Thousands of facilities have found the use of hazardous materials storage lockers (HMSL) or buildings, a cost effective solution to minimizing their risk of environmental contamination. |
Use and Management of Containers
Sub-part I of Part 265 discusses management of containers. Care should also be taken with the containers themselves. Regulations dictate that they be in good condition. Drums should not have bulging heads caused by overpressure. There should be no severe rusting or sharp edged creases or dents, and no structural defects. Drums displaying any of these characteristics should be taken out of service before they begin leaking. If a leak does occur, the container should be immediately over-packed in a salvage drum, or the contents must be transferred to another container.
Some simple precautions will assure the good condition of the drums:
- Store in a weather protected area.
- Never fill a drum beyond 85 percent of its rated capacity.
- Handle and move drums with equipment designed for the task.
- The drum or other type of storage container must be made of or lined with materials that are compatible with the hazardous material to be stored.
The purpose of this is to prevent fires, explosions, gaseous emissions, leaching or other discharge of hazardous waste or hazardous waste constituents which could result from the mixing of incompatible wastes or materials if containers break or leak.
A Proven Storage Solution
Thousands of facilities have found the use of hazardous materials storage lockers (HMSL) or buildings to be a cost effective solution to minimizing their risk of environmental contamination. Because many hazardous materials are also flammable or combustible, the National Fire Protection Association (NFPA) has established standards for these storage units.
According to the 2000 Edition of NFPA 30, a hazardous materials storage locker is a movable prefabricated structure, manufactured primarily at a site other than the final location of the structure and transported completely assembled or in a ready-to-assemble package to the final location. It is intended to meet local, state and federal requirements for outside storage of hazardous materials.
NFPA's regulations, relative to hazardous material storage lockers are found in Standard 30, Chapter Four, Paragraph six.
Where electrical wiring and equipment is required in lockers used for the storage of Class I liquids, it shall be suitable for Class I, Division 2 hazardous (classified) locations.
Electrical equipment and wiring in lockers used for the storage of only Class II and Class III liquids shall be suitable for general use.
The requirements change when dispensing is anticipated in the lockers. The code states: "Where Class II or Class III liquids at temperatures at or above their flash points are dispensed, electrical equipment and wiring shall be suitable for Class I, Division 2, hazardous (classified) locations. In addition, electrical equipment and wiring located within 3 feet of dispensing nozzles shall be suitable for Class I, Division 1, hazardous (classified) locations."
The code also addresses venting requirements when dispensing or filling is performed in a locker. Ventilation at a rate of not less than one cubic foot per minute, per square foot of floor area is specified. Ventilation may be accomplished by natural or mechanical ventilation, with discharge or exhaust to safe location outside the building.
Location, Location, Location
The siting of lockers is governed by regulation. 40 CFR requires ignitable or reactive waste be no closer than 50 feet from a primary building or lot line.
For SI units, 1 foot = 0.3meters; 1 foot^2 = 0.09 meters^2
- If the locker is provided with a fire-resistance rating of not less than four hours and deflagration venting is not required in accordance with 4-4.2.4, all distances required shall be permitted to be waived.
- Site area limits are intended to differentiate the relative size and thus the number of lockers that are permitted in one designated site.
- Distances apply to properties that have protection for exposures, as defined. If there are exposures and such protection for exposures does not exist, the distance shall be doubled.
- When the exposed building has an exterior wall, facing the designated site, that has a fire resistance rating of at least two hours and has no openings to above grade areas within 10 feet (3 meters) horizontally and no openings to below grade areas within 50 feet (15 meters) horizontally of the designated area, the distances can be reduced to half of those shown in the table, except they shall never be less than 5 feet (1.5 meters).
- When a single locker has a gross single story floor area that will require a site limit of greater than 1500 sq. feet(139 meters) or when multiple units exceed the area limit of 1500 sq. feet (139 meters), the authority having jurisdiction shall be consulted for approval of distances.
Design Requirements
NFPA 30, Appendix A-4-6, states that HMSL design features can include but are not limited to the following:
- Secondary spill containment sumps;
- Deflagration venting;
- Ventilation requirements, including mechanical ventilation where dispensing operations are expected;
- Class I, Division I Explosion Proof Electrical Equipment;
- Static Electricity Grounding Systems;
- Fire suppression systems (dry chemical or sprinklers);
- Heavy structural design for:
- Security provisions;
- Doors that lock and permit pallet loading;
- Wind load, snow load and storage load conditions;
- Anchorage provisions; and
- Skid design, permitting relocation using lift truck.
- Fire rated exterior walls, when necessary;
- Interior partitions and divided sumps to segregate incompatible materials;
- Exterior light for area illumination against vandalism;
- Non-sparking floors;
- Shelving;
- Heating or cooling units for chemical stability and comfort control;
- Corrosion protection as required;
- Employee safety provisions (eye/face wash); and
- Hazard signs and signals.
Features provided are determined by specific storage requirements and needs of the owner, keeping in mind the applicable regulations and ordinances that we have examined, along with the approval requirements of the authority having jurisdiction.
Several testing laboratories have developed internal procedures for the examination, testing and listing; or labeling of hazardous material storage lockers submitted by manufacturers. The pre-examination service and the accompanying approval label should provide users a high level of confidence. When making their selection, our suggestion is "Look For The Label."
This article appeared in the October 2001 issue of Environmental Protection, Vol. 12, No. 10, on page 50.
This article originally appeared in the 10/01/2001 issue of Environmental Protection.