Part 2: Prefurbia Incorporates Flow
- By Rick Harrison
- Oct 01, 2010
For the past four decades, the automotive industry has invested billions in fuel efficiency and reducing drag and, at the same time, significantly added to the average engine horsepower. While government has focused on the vehicle, no steps have been taken to make neighborhood streets more efficient.
The management of a new era of design dedicated to reducing time and energy while transiting through a neighborhood is called "flow." In Prefurbia, flow is essential to neighborhood sustainability.
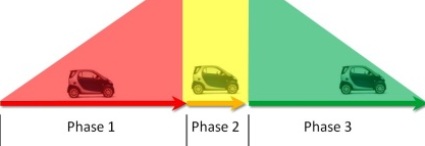
Getting a vehicle in motion (Phase 1), cruising (Phase 2) and stopping or slowing (Phase 3) are the three phases of a “segment cycle.” A segment begins upon entry to a street and ends when a driver stops or slows down to turn or enter another street. Phase 1 involves the time and energy needed to get a one- to two-ton (or more) vehicle moving from a stop to a target residential speed. In some areas, this could be from 20 miles per hour to 30 mph. Phase 1 consumes the most energy and typically the most time. Phase 2 uses the least time and less energy than Phase 1. Phase 3 consumes almost as much time as Phase 1, but with new braking technology, this phase can actually generate energy. Reducing the number of Phase 1 segments lowers the amount of energy consumed. Similarly, reducing the number of Phase 1 and 3 segments also shortens the time needed to travel.
At 30 mph, the distance needed to accelerate and then stop comfortably is about 400 feet.
In traditional planning processes, designers give little (if any) attention to the flow of traffic. Very few homes are located on an entry street, requiring 90 percent of the residents to travel a minimum of two segment cycles. About half the residents have to use three segment cycles to reach their homes. In Prefurbia, most residents can get home with just one segment cycle, and only a few others have two segment cycles.
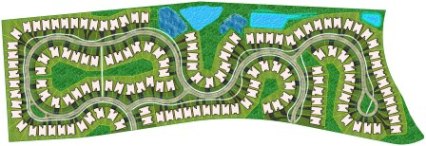
The length of Phase 2 is critical. In the conventional subdivision, for the most part, the distance along each segment cycle is quite short with some so small that Phase 2 is never reached. This design may be so inconvenient from a flow standpoint that the driver is "encouraged" to accelerate to make up for the time. Segment cycles within the Prefurbia neighborhood are long, enabling a driver more time in Phase 2.
Note the cul-de-sac on the right in Figure 3. Why didn't the designer reverse the street to loop the cul-de-sac the other way, reducing the segment length from the entry to the end of the cul-de-sac? Prefurbia is a balance of economics, environment, and existence so the designer must weigh each benefit and derive a design that serves each of the three “Es” well. In this case, the geometry of the area better achieves efficiency with the current configuration. Also, having an intersection serving 30 homes as soon as a driver enters the neighborhood is not the best for safety. On the other side of the site, there is such an intersection but it serves fewer lots. Finally, the cul-de-sac provides a nice entrance void of street intersections. The homes pulled away from the street give the impression of low density. If a street was placed at this point, entering the neighborhood would not have this welcome feel.
In Prefurbia, designers use [www.performanceplanningsystem.com/trafficdiffuers] traffic diffusers, which maintain flow on the primary traffic street while providing the functionality of a roundabout.
From a pollution standpoint – addressing the auto industry without addressing planning is like requiring frosting to have no calories yet use the frosting on a high fat, sugar laden cake
Reducing environmental impacts
Prefurbia reduces waste and employs more efficient forms of design. The method represents a reversal of how technology in land development is used, replacing lots per minute (LPM) automation with the art of neighborhood design. It’s time for technology to be used to construct great neighborhoods for families to thrive. By exceeding the minimums, designers can deliver economic and environmental advantages.
There are only a few situations in which a tight grid pattern designed to minimums is the optimum solution from a geometric perspective. Such a site must closely conform to the dimensions needed to stack lots, with a fairly flat topography and long blocks that have few cross streets.
Here are a few examples that demonstrate better efficiency gains through design.
Figure 1 shows two cul-de-sac’s side by side. Both use the following minimums:
- 25-foot front yard setback,
- 5-foot side yard setback,
- 80-foot lot width at the setback, and
- 60-foot cul-de-sac minimum radii.
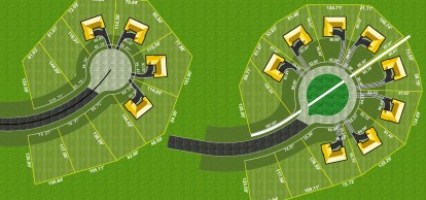
The conventional subdivision (left) has four premium lots with larger rear yards. The lots are set along a street void of traffic, which are the two main features that make a typical cul-de-sac lot demand premiums. The distance between home fronts is a minimum of 170 feet face to face, providing a feel of very low density.
With 8,500 square feet of paving, serving very few lots, standard cul-de-sacs are terrible for the environment and very inefficient. Four 80-foot-wide standard lots facing each other would need only 4,800 square feet (160 x 30) of street paving. The conventional cul-de-sac in this case is 44 percent less efficient, requiring that much more in paving costs and environmental impacts. Snow removal for those that live in the north and municipal costs to maintain those premium lots are both 44 percent greater.
Exceeding minimums can seem magical. The second cul-de-sac (right) exceeds the minimums. The end circle is greater with a 160-foot (versus 120 foot) diameter, and the homes are set back further than the minimum. The lot width at the front setback line remains at the 80-foot minimum. The street along the cul-de-sac is different, now a one-way street because that is how people drive along a cul-de-sac and a larger radius justifies a one-way lane with a central landscaped park.
Instead of 8,500 square feet of paving, this cul-de-sac has 7,400 square feet (13 percent less) serving eight instead of four premium lots. Eight standard lots along a street facing each other would require 9,600 square feet of paving. By exceeding the minimums, the designer increased efficiency by 23 percent over standard rectangular lots. The central island can be used for a neighborhood park or for rain gardens, or a combination to further add character and reduce environmental impacts. When the island is used to filter stormwater, there would be no mountable curbs to pay for, reducing costs even more.
A wide walk extends through the neighborhood. The driveways become longer, but they are tapered and use the Prefurbia method of sculpting with organic lanes, so they consume similar surface area to a standard driveway, even though they are longer.
Density is a function of how many lots a designer can fit along the front setback line. In order to stretch the front setback length to gain density (when the minimum setback guarantees the front of the home is exactly parallel to the curb), the designer also must stretch the street. To gain density, the designer consumes the site with street, which is a poor choice for the environment and economics.
The cul-de-sac example increases the setback depth, which is still somewhat concentric to the traffic circle. With Prefurbia, designers can totally separate the relationship between front setback and street where road paving, walks, and homes all form their own organized sculpted shapes.
Coving is the first organized planning method that separates the rigid parallel relationship between the front of the home and curb of the street. Efficiency varies, but a 25 percent gain in efficiency compared to conventional design is about the average. Imagine a world with 25 percent less construction costs and environmental impacts. An organic free-form design will almost always conform to the natural surface area much easier than a rigid pattern. With the gain in efficiency, monotony is a thing of the past, each lot takes on a unique shape making it virtually impossible to utilize a LPM technology.
About the Author
Rick Harrison is president of Rick Harrison Site Design Studio in Minneapolis, Minn.