Avoiding Oxidizer Blues
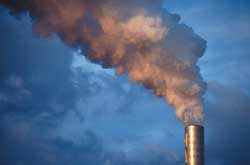
To control volatile organic compound (VOC) emissions and hazardous air pollutants (HAP), environmental health and safety (EHS) and pollution control professionals in the surface coating, chemical, pharmaceutical, refinery, electronic, semi-conductor, remediation and many other industries rely importantly on the nearly one billion dollar domestic thermal/catalytic oxidizer industry. Selecting oxidizer types with widely varying features, options and proper sizing requires extensive process knowledge and comprehensive planning. There are many perspectives to reconcile into the design requirements of an oxidizer system. High temperatures and corrosive compounds present challenges to system longevity and fuel economy. Accordingly, some system owners report that their systems have failed to meet their expectations.
This guide addresses the common oxidizer woes and offers practical advice prior to and following an investment.
My Oxidizer Supplier is Out of Business
The historic Clean Air Act Amendments (CAAA) of 1990 launched a "Klondike" rush to garages all over America and spawned literally hundreds of oxidizer designs and regional builders. Just 12 years later, acquisition, the economy and competition have taken an inevitable toll, leaving many system owners with problems, but without recourse. There are significantly fewer providers today than 12 years ago. No one who is dependent upon oxidation to meet their air pollution control requirements wants to get caught in the bind of another company going out of business.
Investigate the potential oxidizer company before you purchase your system. How long has the potential supplier been in business and what is their reputation? Are they willing to supply you with recommendations? Are they offering to show you some of their installations?
Determine the company's after sale field service capability. How large is their service department or do they even have a field service department? What is their response time in the case of an emergency outage or shutdown? Does the field service department offer monthly, quarterly, semiannual or annual service contracts for the oxidizer? Does the supplier provide 24-hour, seven days per week service? Ask their references these questions.
In the early planning stages for your oxidizer procurement, it is advisable to hire a consultant to independently measure your flows and determine the VOC species that will have to be processed by your oxidizer. |
I Outgrew My Oxidizer's Capacity
The oxidation industry's number one source of new business each year is size replacement or upsizing for higher plant/process capacity. Bet on your own success and anticipate ever-tightening emission regulations. The cost to replace or upsize is frequently two and three times the modest incremental cost at the outset to build-in expandability. Some suppliers offer extensible designs or modularity. Expect to grow and design accordingly.
Plan, specify, design and construct your new oxidizer, checking everything at least twice. One common occurrence is setting up to destroy one type of VOC species and the actual process fume stream is changed or varies. In the early planning stages for your oxidizer procurement, it is advisable to hire a consultant to independently measure your flows and determine the VOC species that will have to be processed by your oxidizer. Some of the oxidizer venders will perform these tests as an incentive to buy their product. There are outside consultants that can perform the same verification tests. Don't rely on just one source to generate your specifications, there is too much at stake.
We Have Too Many Shutdowns
Many industries require process or production dependability where good warranties and fast service are frankly, "too late." Any unplanned shutdowns are costly and disruptive. Discuss critical component "redundancy," scheduled maintenance, warning devices, operator training and troubleshooting and service hotlines with your potential supplier. Reliability is often sacrificed when price competition is stiff.
If your answers to the following questions are "YES," then there are some critical considerations you must confront.
- If your oxidizer shuts down, will your plant have to shutdown or suspend operations until the unit is brought back on line?
- Will you be subject to a reprimand or fine from the regional Air Quality Management District or the state environmental agency if the oxidizer is shutdown and you continue with the plants operations?
Solutions begin at the design stage. Incorporating redundant systems into the design that takeover if one component fails is the common answer to this problem.
Our Operating Costs are Higher Than Expected
The * fuel value of your process air, supplemental fuel prices, burner efficiency, system integrity, destruction removal efficiency (DRE), excess air -- all impact operating costs. Experienced suppliers will assist you in optimizing these often-conflicting factors. For most, oxidizer designs offer an air-to-air heat exchanger option to preheat the process stream: their efficiency varies from 50 to 85 percent; the higher their performance, the higher the capital cost. There is other capital vs. operating cost "trade-offs" you will want to discuss with your supplier. It is very useful to make long-range process and planning assumptions in discussing these trade-offs. Generally speaking, lowest operating costs are achieved through superior designs and capital features.
* For charts to assist in calculating fuel costs, refer to www.alzeta.com click on "products" and select oxidizer type (catalytic, thermal) to proceed.
The oxidation industry's number one source of new business each year is size replacement or upsizing for higher plant/process capacity. |
Our Catalytic Oxidizer is Working, But...
The economies and many other advantages of catalytic oxidation are so desirable that limitations are often downplayed. Burners and heat recovery are still core design considerations; treat the project as a thermal oxidizer with a catalytic feature. Catalyst damage can be costly if not anticipated ("masking", poisoning" and other thermal effects). Halogen containing compounds, such as HMDS and "spin-on-glass," pose special problems. If harmful compounds cannot be "slip-streamed" to bypass the catalyst, catalytic oxidation is not for you. Preventive maintenance schedules can be made more vigilant when harmful materials are present.
My New System Was Too Big/Small From the Beginning
Adequate system sizing criteria is more easily mistaken than anyone would expect. Manufactures are obliged to provide what they are asked to provide and are commonly to use the information given. Process "spikes" can often overrun the systems capacity. Inaccurate stream information will invariably come back to haunt the company. If process spikes are possible then the oxidizer must either be sized big enough to handle them or you will have to provide some sort of capacitor to even out the spikes.
It may serve to rent or lease an oxidizer prior to purchasing one. This option allows you to determine if there will be any anomalies in the process that could damage a new oxidizer and allow you to deal with the trouble before you commit to ownership.
"VOC/HAP Destruction is Disappointing, ? I'm Perpetually at Odds with Enforcement Agencies"
Destruction rate efficiency (DRE) is a true science and meeting ever increasing regulatory requirements is often a challenge, after the system is delivered. It's always a good idea to require excess DRE in the original design criteria. Many things can effect system efficiency, such as damaged equipment improperly sized equipment, improper application of equipment, and improperly run equipment. Worst of all would be the situation where your oxidizer company was unable or unwilling to stand behind their product and make it work at all possible cost. All of these can be offset by surplus efficiency. This practice also puts operators in "positive stead" with regulators and local citizen groups. It is a tangible benefit to operate in excess of DRE expectations.
Your choice of companies can determine the potential for a successful outcome. Most companies have a track record of their DRE achievements and are willing to share this information. It is recommended that you choose a company who has regularly achieved better than required DRE.
This article appeared in the July/August 2002 issue of Environmental Protection, Vol. 13, No. 7, page 28.