Water Reuse: Reclaiming a Finite Resource -- Part II
- By Mike Studer
- Feb 01, 2002
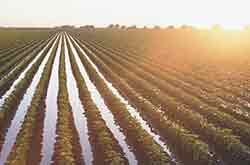
This is the second in a two-part series on water reuse. Part I, featured in the July 2001 issue (see Archives at www.eponline.com), focused on the rationale for recycling water and the laws that pertain to water reuse. Part II deals with treatment technologies used in water reuse.
Treatment Technologies
The treatment technologies used in recycling water are those of conventional and advanced wastewater or water-supply processes -- or offshoots thereof. For example, during recharge to groundwater for later extraction, recycled water must meet standards under the Safe Drinking Water Act (42 United States Code (USC) 300f-300j-26). The recycled-water treatment process therefore might comprise one or more of the following: ballasted flocculation, single- and two-stage biologically aerated filtration, membrane-bioreactor treatment, microfiltration, continuous up-flow filtration, nanofiltration and reverse osmosis. Granulated active carbon (GAC) and electro-technologies also might find use.
High-quality monitoring of such treatment processes is essential. On-line analyzers are used to measure such parameters as turbidity (an indicator of potential biological problems), ammonia (NH4), phosphates and nitrates.
Secondary Treatment
Most recycled water sourced from publicly owned treatment works (POTWs) receives, at a minimum, biological (secondary) treatment to remove dissolved organic matter using one of three systems: fixed film, suspended growth or lagoon.
- Lagoon systems are shallow, wastewater-holding basins that allow for the natural biological degradation of sewage over a period of several months.
- Fixed-film systems grow microorganisms on substrates such as rocks, sand or plastic, with wastewater passing through the substrate.
- Suspended growth systems suspend microorganisms in wastewater, which grow in size and number before settling out as sludge.
Invariably, one or more forms of disinfection follow biological treatment. They include chlorination, ultraviolet (UV) irradiation and ozonation.
Advanced Treatment
Advanced treatment sometimes is needed to remove other unwanted constituents from wastewater. Primarily, they include separation systems that rely on physical, chemical, electrical and thermal principles.
- Chemical
-- Some systems deliver additives that help remove such constituents as phosphorus and nitrogen. Ion exchange is chemically based and applied to reduce total dissolved solids, hardness, alkalinity and silica levels.
- Physical
-- Physical means comprise such mechanical devices as centrifuging and air stripping (which can be practical for, for example, removing NH4) as well as adsorption by activated carbon (which is most effective at removing non-ionic organic material).
- Electrical
-- Although membrane separation for the most part classifies as physical treatment, it can be combined with electric potential to filter small (down to molecular-size) particles from water.
- Thermal
--Thermal processes can rid water of most suspended and dissolved matter.
Membranes commonly find use in a number of process industries, including chemical, food, pulp and paper and power generation. The established genre of commercially available membrane systems comprises microfiltration, ultrafiltration (UF) and reverse osmosis (RO) -- each treating a different particle-size range. RO removes, to varying extent, all types of contaminants. Recent membrane systems include centrifuging and vibrating designs -- both intended to limit buildup of performance-interfering solids along membrane surfaces.
Other special membrane-separation processes include pervaporation (which separates the more volatile compounds from a liquid into a gas) and electrodialysis, which separates ions from a solution across an electrically charged membrane.
Centrifuging using one or more of several available designs, or mechanical methods, is useful for oil/water separation and for large- particle separation (solids of particles sizes ranging from one to 5000 microns). Particles greater than 5000 microns (five mm) may require pretreatment before centrifuging. Another mechanical method applies acoustic energy to enhance the rate and efficiency of separation.
Activated carbon generally is used in combination with other treatment processes and is effective until it becomes saturated, after which it is replaced with regenerated or virgin material.
Thermal -- Counted among these expensive but effective purification systems is a variety of distillations, including multi-stage flash, vapor compression and multiple effect.
Ion exchange --Total deionization can be achieved with frequent resin regeneration. Continuous deionization can be achieved by packaging the elements of electrodialysis and ion exchange as several membrane cells sandwiched between two electrodes. The electrodes split water at the end of the cell allowing for the regeneration of the ion-exchange resin. A process patented by the Lawrence Livermore National Laboratories (LLNL), based on what the lab calls capacitive deionization, draws ions out of the water and onto aero-gel plates based on their charge.
A Sobering Note
Despite recycled water's growing acceptance and use and a general understanding that the technology can, at a cost, meet most any standard, there is concern that reclaimed water may lack the history of safe use that most conventional sources have and may contain unknown or unquantified contaminants. Also, institutional barriers, as well as varying agency priorities, have been -- and continue to be -- obstacles to unchallenged implementation of water-recycling projects.
References
William D. Ruckelshaus. McGraw-Hill Recycling Handbook, 2nd Ed. Herbert F. Lund, editor. New York.1998
Chin, K.K. and Kumarasivam, K. Industrial Water Technology: Treatment, Reuse & Recycling. Elsevier Publications, Amsterdam, New York, London. May 1986
This article appeared in the February 2002 issue of Environmental Protection, Vol. 13, No. 2, page 22.
About the Author
Michael A. Studer, VP marketing, has been with L-3 Communications Infrared Products and its predecessor, Raytheon and Texas Instruments, since 1982 in various manufacturing, engineering, and account management roles. Studer has six years of thermal imaging market and production experience and is a TI Certified Six Sigma Black Belt and a Raytheon Certified Six Sigma Expert. His current responsibilities are market and competitive analysis, product strategy and positioning, marketing communications, and market expansion opportunity analysis. Studer has a BS in industrial engineering from Iowa State University. He can be reached at (972) 344-4000.